Professor Koren is credited with conceiving the RMS paradigm and inventing its major technologies. Consequently RMS became a new international research discipline with many practical implementations. No wonder that Koren is recognized as “the Father of Reconfigurable Manufacturing.” In the early 1990’s Koren predicted that globalization would become a major factor in industrial competition, making the ability to respond rapidly to changing markets a vital goal for industry. Hence Koren added Rapid Responsiveness to the two traditional goals of production: Low Cost and High Quality. In 1995 he wrote to NSF a proposal to establish an Engineering Research Center (ERC) for Reconfigurable Manufacturing Systems that their architecture is designed to be responsive to abrupt market changes, and is based on six RMS characteristics, as shown below.
The NSF-sponsored ERC for Reconfigurable Manufacturing Systems was launched on August 1, 1996 (Koren’s birthday; a nice birthday gift 🙂 ). Koren became the ERC Director and stayed as the Center director until 2012. The ERC-RMS is regarded by NSF as one of the most successful ERCs, because of its unprecedented impact on the profession and the manufacturing industry. Several RMS methods and technologies were implemented in factories. You may see examples in Roman Krygier’s speech (see Special Events) and in the Quotes.
A responsive production system must be designed for rapid scalability in its output that allows producing the products at higher speed to match production rate to increased market demand. The system must be convertible from one product to another that customers like more. The system must have in-line diagnosability to guarantee the output production of 100% good quality products. For example, the RIM (Reconfigurable Inspection Machine) that was invented by Koren does successfully this mission.
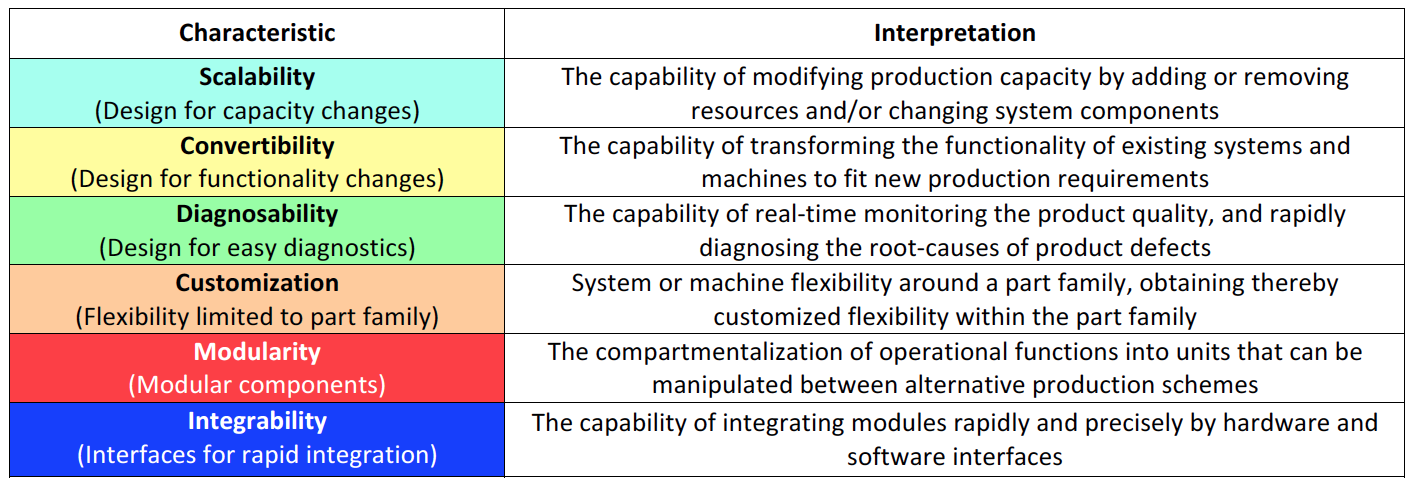
A schematic diagram of a typical RMS architecture is shown below. Capacity scalability is achieved by adding machines into existing stages without changing the basic architecture of the system.
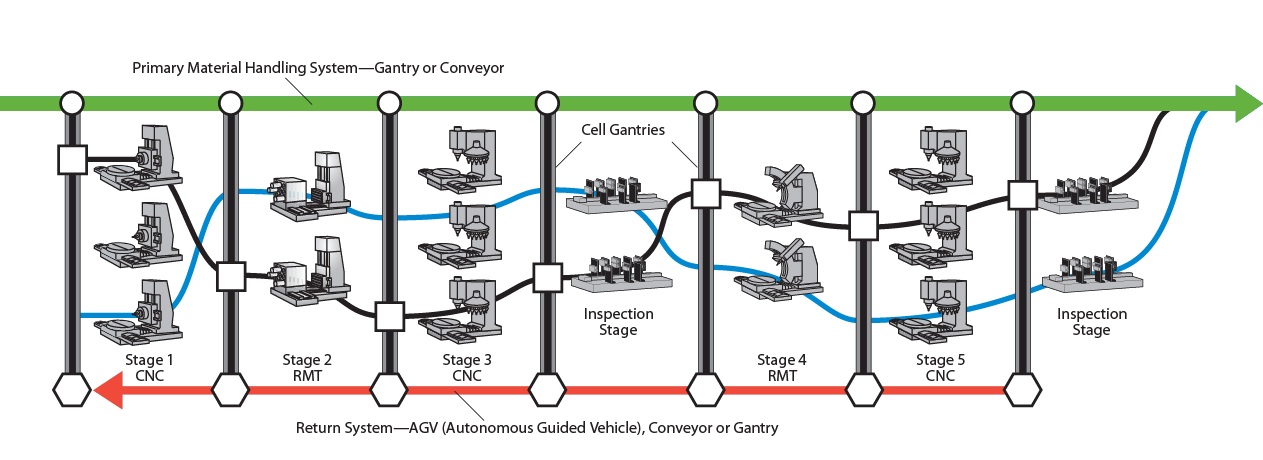
A typical RMS architecture
Koren is the inventor of the three major U.S. patents that define the RMS paradigm: The whole reconfigurable system, the Reconfigurable Machine Tool (RMT) machine, and the in-line inspection method and inspection machine. These three principal patents define the major scope of RMS and explain how to implement the RMS technology. He also holds additional four patents in various RMS technologies (see the section on Patents in this website). Reconfigurable systems are based on Koren’s design principles and reconfiguration technologies that increase the speed of responsiveness of manufacturing systems to market changes, a technology that is critical in the current environment of global competition. Koren has led the implementation of RMS and their associated technologies in industry. His seminal 1999 keynote paper “Reconfigurable Manufacturing Systems”, has received 1,400 scientific citations, and has established RMS as a new, worldwide research discipline. As an evidence to the last claim we display below data that show that until 1996 when the RMS center was established there were only 10 papers that included the term “reconfigurable manufacturing” (mostly in computer science). Because of Koren’s influential research and three Reconfigurable Manufacturing international conferences that he organized in Michigan (in 2001, 2003, and 2005) this number increased exponentially to 500 in 2006, to 4,000 in 2011, and to 100,000 in 2014.
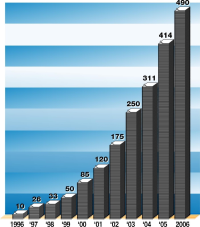
Number of papers that include “Reconfigurable Manufacturing”
Koren is the inventor of a new generation of manufacturing tools —Reconfigurable Machine Tools (RMT) that reduce cost for low-volume manufacturers. He is an inventor on the RMT patent, and he led the team that built the world’s first industry-scale RMT (photo below). Koren also holds a U.S. patent on “Reconfigurable Inspection Machines (RIM)”, and he built the world’s first RIM for in-line inspection of engine block porosity defects, a machine that was integrated into industry high-volume engine-block production line to enhance product quality.
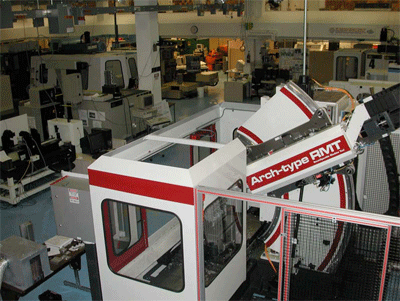
The Arch-type Reconfigurable Machine Tool (RMT) at the ERC-RMS Testbed (in the background); the design is based on Koren’s RMT patent.
Koren’s team developed a reconfigurable machine-vision system for in-line surface porosity inspection of engine blocks that was integrated into production line. The system utilizes his specially designed vision system to acquire high-resolution images of the block surface, which are then analyzed to detect, locate, and measure pores (small pits < 1mm that are on the surface; resulted in by the casting). This technology is very important to engine manufacturers because of the difficulty in objectively measuring the sizes and location of irregularly shaped surface pores, and doing it at production line rates (20 seconds). In 2006 General Motors installed Koren’s in-line surface porosity inspection system at its engine plant in Flint, Michigan. The inspection system was integrated into the production line, and a conveyor moves all engine blocks through this inspection station. Namely, every engine block is measured within 20 seconds. By using this technology GM prevents defective parts from reaching the customers.
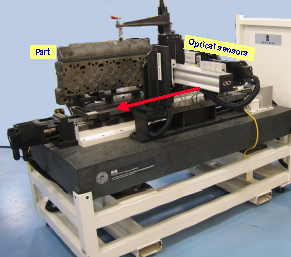
The prototype of the Reconfigurable Inspection Machine (RIM)
The ERC designed and demonstrated an Intelligent Autonomous Guided Vehicle (AGV) that moved fast, but ensured safe movement of people on the factory floor. (This AGV operated with the CARMEL algorithms. See Koren’s Robotics research).
The ERC-RMS financial support during the period 1996–2011 was $47 million, obtained from government and industry sources. The ERC-RMS Center under Koren’s leadership graduated 70 Ph.D. students and 270 Masters students, many of whom are working now in the U.S. industry and national labs, and 12 Ph.D. graduates became professors at universities in North America. Koren discusses the reconfigurable manufacturing paradigm and technologies in his book The Global Manufacturing Revolution: Product-Process-Business Integration & Reconfigurable Manufacturing (Wiley, 2010).
Independent External Evaluation In May 2007 the National Science Foundation formed an independent national industry-academic review team to evaluate on-site the ERC-RMS accomplishments since its formation in 1996. Below are three conclusions of the NSF Site-Visit Report:
“There is strong evidence of the effectiveness of both the vision of the Center director and the ability of the director to execute the vision.” (The Center Director in 1996–2007 was Yoram Koren)
“The Center has substantially increased awareness of the importance of reconfigurability as an enabling technology for realizing flexible quantity and quality production, and created tools for executing these systems.”
“The physical manufacturing research infrastructure developed by the ERC-RMS is unique in the US. No other university in the US has space, and experimental equipment like it, and it is one of the best in the world.”